How safety shoes are made?
Design and Planning
The first step in producing safety shoes is to start with design. A good design should not only consider the appearance of the shoes, but also ensure that the shoes meet specific safety standards and functions.
• Safety standard considerations
Safety shoes must meet the safety standards of different countries and industries, such as the ASTM F2413 standard in the United States and the EN ISO 20345 standard in Europe. Please refer to the safety standards of various countries below: Safety shoes anti-smashing steel toe: steel toe type, safety shoes anti-smashing steel toe standard
• Functional design
Design various protective functions for different styles of safety shoes, such as impact resistance, puncture resistance, slip resistance, oil resistance, high temperature resistance, waterproofness and anti-static.
Material selection
• Upper material
The material of the upper is usually leather, synthetic fiber or mesh fabric. The advantages of leather are wear resistance and breathability, while synthetic materials are lighter and suitable for long-term wear.
• Toe material
The protective toe of safety shoes is crucial and is usually made of steel, composite materials or aluminum. Steel toe caps offer the strongest resistance to compression and impact, but are heavier; composite materials are lighter, but still offer good protection, and are non-conductive, making them suitable for electrically hazardous environments; aluminum toe caps also offer lighter toe cap options, suitable for positions that require weight reduction.
• Sole material
The material of the sole directly affects the shoe’s anti-slip, wear-resistant and protective properties. Common materials include rubber, polyurethane (PU) and thermoplastic polyurethane (TPU). Rubber soles are known for their anti-slip and durability, making them suitable for wet or oily environments; PU soles are lightweight and elastic, making them suitable for long walks; TPU has better wear resistance and durability.
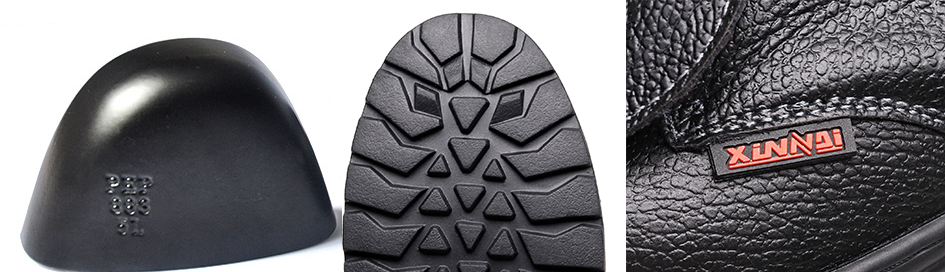
Cutting materials
Use cutting dies or automatic cutting machines to cut large pieces of leather, synthetic fibers or mesh fabrics into precise upper parts. When cutting, take into account that different parts of the upper require different material thicknesses and elasticities
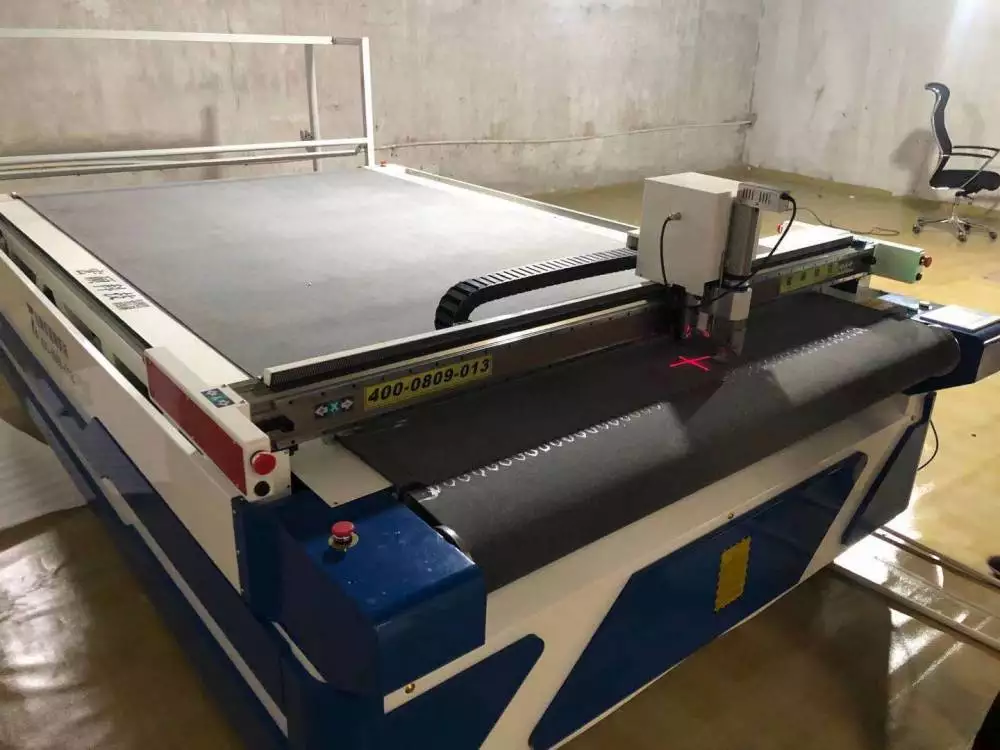
Toe cap insertion
Add a protective toe cap to the front of the vamp. The toe cap must be precisely fixed to ensure that the shoe can provide adequate protection when encountering heavy objects or impacts. The toe cap insertion process for different materials is slightly different. Steel toe caps may require more reinforcement, while composite toe caps require special heat bonding technology to ensure that the toe cap is tightly bonded to the upper.
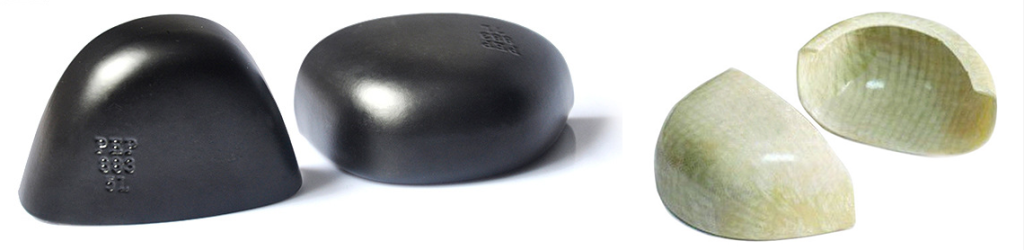
Sewing and upper assembly
The upper parts are connected together through high-strength stitching to ensure that the shoes will not crack or damage during long-term use. If the safety shoes need to be waterproof, a waterproof membrane or sealant will be added during the stitching process of the upper.
Insole and midsole installation
The use of ergonomically designed insoles provides arch support and absorbs vibration and pressure on the foot during work. When the midsole is added to provide puncture protection, the puncture-resistant midsole (such as steel or Kevlar) will be sandwiched between the insole and the sole to prevent sharp objects such as nails from penetrating the sole.
Sole fixing
There are two common processes for installing the sole: cement process (bonding) and direct injection molding process. In the cement process, the sole is bonded to the upper with a high-strength glue, which is simple and flexible; in the direct injection process, liquid rubber or PU material is injected into the mold, and the sole and upper are directly combined together at high temperature, providing stronger bonding and durability. The design of the sole focuses on functionality, usually including anti-slip patterns, oil and chemical resistance, and electrical insulation.